‘What prop should I choose that will make the most thrust for my airboat’?
Step 1: Horsepower. Sometimes people get hung up on engine Torque vs HP, and are not sure which is most important. In truth, HP is simply a mathematical calculation of Torque and RPM – so HP is Torque with RPM. Without RPM, Torque is meaningless. The formula for HP is simply (Torque x RPM)/5252. Horsepower can be explained as the amount of work done in a given amount of time. Since the engine’s Torque curve doesn’t change linearly as the RPM changes, higher RPM means there’s more work being done every minute even if Torque is flat or decreasing. If you’ve ever looked at an engine dyno sheet, you’ll notice that the HP curve and the Torque curve always cross at 5200 RPM – this is because HP is mathematically calculated from Torque. So, Step 1 – determine max available Horsepower from the engine.
Step 2: RPM. RPM can be divided into 2 categories: Direct-Drive and Reduction-Drive. For direct-drive applications, the maximum engine RPM and maximum propeller RPM will be the same. For direct-drive aircraft engines, these were designed to develop peak HP at 3000 or less RPM with the RPM limitations of propellers in mind. For automotive engines, the choice to use them as a direct-drive application means the HP will be limited to what is developed at 3000 RPM – typically this number is half of the peak HP specified for the engine.
Because automotive engines were never designed to drive a propeller, the peak HP is typically developed at a far higher RPM than any propeller can efficiently (or safely) turn. For this reason, reduction units are used to allow the propeller to turn at an efficient RPM while allowing the engine to develop peak, or close to peak HP. For reduction-drive applications (typically automotive engines and some aircraft engines), the target max engine RPM of the engine should be identified before selecting the reduction ratio. For aircraft engines using a reduction, this is pretty straight-forward. For automotive engines, this is a subject that must take into consideration the “reasonable” maximum engine operating RPM. Reasonable means that even though the engine might make peak HP at 6000 or higher RPM, that may not be practical for several reasons including engine longevity. I suggest big-block engines target in the neighborhood of 5000 RPM (+/-) and the newer small-block LS type engines might target 5200 to 5600 RPM for getting most of the available HP. Ultimately, this is your choice based on your engine and your personal comfort level.
Selection of the reduction ratio is the next step in RPM, once the max engine RPM has been identified. For example, most big-block engines that will only turn 5000 RPM, some of the best all-around ratios fall in the range of 2-to-1 or the popular 2.3-to-1 variations. This means the propeller RPM will be 2500 RPM or 2170 RPM respectively. For engines that plan to turn higher than 5000 RPM, the better ratios are 2.3 or higher (2.5 or 2.68). There is much deeper discussion to be had regarding ratio selection that I wills save for another article. In general, the higher the ratio, the lower the maximum propeller RPM and this will bring in to consideration another factor of dynamic pressure and propeller efficiency that requires more blade area than a higher RPM would require for the same HP output.
Note on the Importance of Max Propeller RPM Limit: When a propeller is turning at full RPM, the centrifugal forces are trying to pull the blades out of the hub. These centrifugal forces acting on the blades increase by a squared factor (non-linear) with RPM. Think of the force of a large pick-up truck swinging of the end. Exceeding the max propeller RPM by 10% is serious and requires the propeller to be inspected. Exceeding the max propeller RPM by 20% could be catastrophic to the propeller structure. Propeller overspeed is serious and can lead to catastrophic failure, injury, or death.
Step 3: Propeller Size. Once the max HP and max RPM for the propeller have been identified, the propeller size can be selected. Propellers can be sized using 3 primary variables: Blade Length, Blade Width, and Number of Blades.
For direct-drive applications, the most common diameter is 72” or less – with the occasional 74” option. This size range is due to the higher 3000 RPM operating limit of direct-drive engines. For direct-drive applications, we offer the CarbonMax™ standard (11” wide) and Narrow (10” wide) in diameters from 66” up to 74”.
For reduction-drive applications, the most common diameter is 78” or larger. We offer a range of blade sizes to work with to accommodate up to 2700 propeller RPM. We offer the 12” wide CarbonMax 2.0 in diameters from 76” to 82” that are best for most 2-1 and some 2.3 or higher reduction ratios. We offer the 13” wide CarbonMax™ EX and the 15” CarbonMax™ SW in diameters from 77” to 84” for 2.3 and higher reduction ratios. The larger the diameter and wider the blade, the lower the maximum RPM – these longer, wider blades were designed to compensate for those larger reduction ratios to boost efficiency, but also happen to be quieter due to the slower turning propeller RPM.
If these 3 Steps in Propeller Sizing have been identified correctly, the propeller selected will ensure you get the absolute maximum amount of Thrust available at your target maximum RPM. We have designed each propeller blade style to allow a custom sizing option for a range of HP and operating RPMs. If your propeller is sized right, your blade angles will end up in the correct range once you set them for your target RPM, and you will know that you are making the most lbs of Thrust per HP possible.
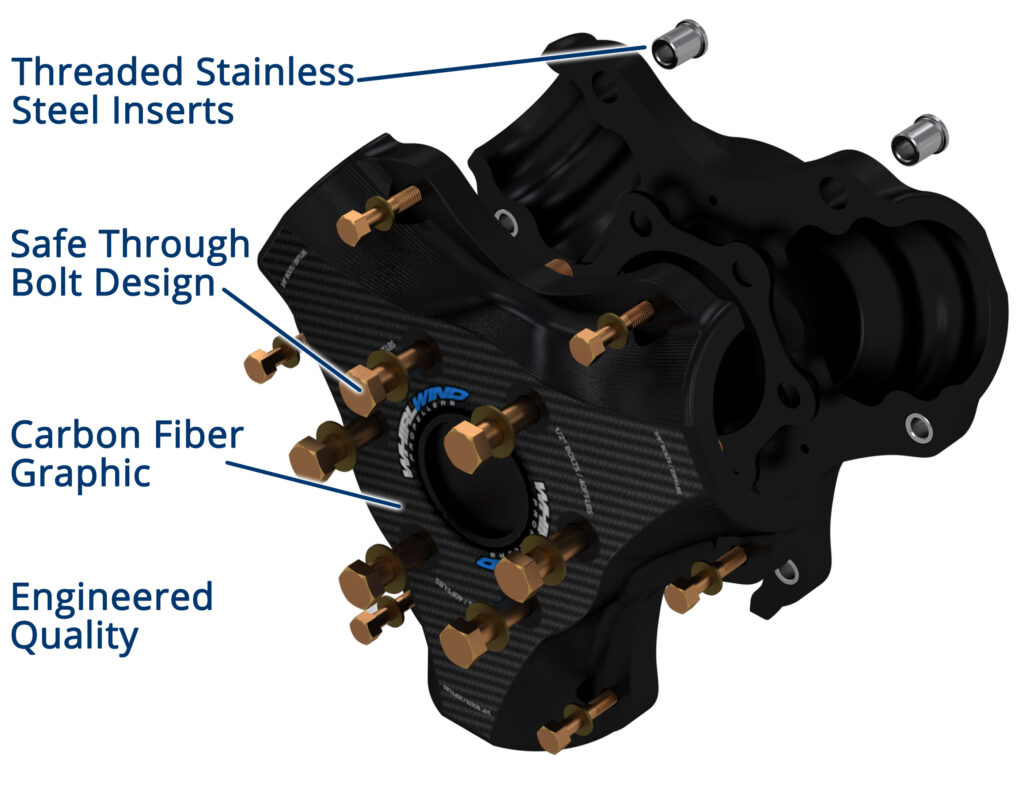
To take out the guess work, we have designed our CarbonMax™ propeller systems to be very user friendly with the pitch setting range already engraved in the QuickChange™ hubs. If you do not end up pitched in the correct range, then you know you need to change your propeller selection.
So now that we’ve covered a little, or perhaps a lot of the science, hopefully this has been beneficial to understand some of the basics of propeller sizing. We have designed the wide-blade CarbonMax™ series to be the most advanced composite adjustable propeller system while also being user friendly. Our CarbonMax™ blades feature an electro-formed Nickel leading edge shield so you get a superior damage-resistant prop and a longer service life which is important for the harsh conditions that airboats operate in.
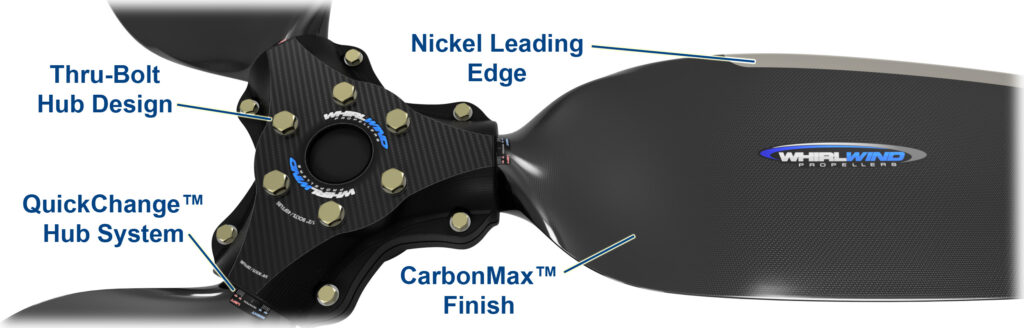
Our QuickChange™ Hub was developed over 20 years ago with a through-bolt design to give you the highest level of safety and strength possible. The QuickChange™ hub has an integral blade pitch guide right on the hub that makes it a breeze to set-up.
Whatever your airboat mission (work, pleasure, hunting or otherwise), we can guarantee that we have the right propeller for your airboat.